Root Cause Analysis Template Guide
- Michelle M
- Mar 3
- 4 min read
Root Cause Analysis (RCA) is an essential problem-solving methodology used to identify the underlying cause of an issue, rather than just addressing its symptoms. Whether applied in business, healthcare, manufacturing, IT, or any other industry, RCA helps organizations understand why problems occur and how they can be prevented in the future.
In this blog, we will explore the significance of RCA, different methods used, and how to structure an RCA template to ensure thorough and effective problem resolution.
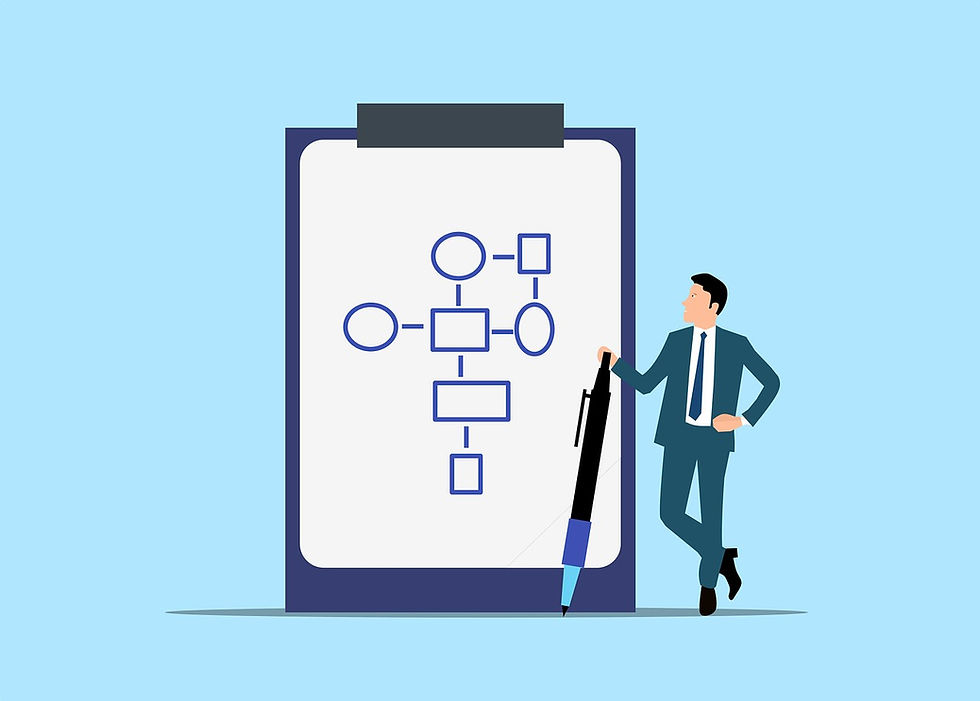
Understanding Root Cause Analysis (RCA)
Root Cause Analysis is a systematic approach to identifying the primary cause of an issue. It involves investigating an incident, process failure, or defect to determine the factors contributing to it. By addressing the root cause instead of the surface-level symptoms, organizations can prevent recurring problems and improve overall efficiency.
Why is RCA Important?
Prevents Recurrence – Fixing the root cause ensures that the problem does not happen again.
Saves Costs – Eliminating recurring issues reduces downtime and saves money.
Improves Productivity – Resolving core issues enhances workflow efficiency.
Enhances Customer Satisfaction – Consistent quality improvement leads to higher customer trust.
Strengthens Risk Management – Identifying and mitigating risks proactively prevents future disruptions.
Key RCA Methods and Techniques
There are various methodologies used for Root Cause Analysis. Each method has its strengths and is suitable for different scenarios.
1. The 5 Whys Technique
This method involves repeatedly asking "Why?" to trace the root cause of a problem. Typically, asking "Why?" five times is sufficient to identify the underlying issue.
Example:
Problem: A manufacturing machine stopped working.
Why? The motor burned out.
Why? It overheated.
Why? The cooling fan was not working.
Why? The fan belt was broken.
Why? It was not replaced during maintenance.
The root cause here is a failure in maintenance procedures.
2. Fishbone Diagram (Ishikawa Diagram)
This visual tool categorizes potential causes into branches to explore various factors that might contribute to a problem.
Categories often include:
People
Processes
Materials
Machines
Environment
Management
This technique helps teams brainstorm multiple contributing factors to a problem.
3. Failure Mode and Effects Analysis (FMEA)
FMEA is a structured approach to analyzing potential failure points in a system. It assesses:
The severity of a failure
The likelihood of occurrence
Detectability
This method helps prioritize which issues need urgent attention.
4. Fault Tree Analysis (FTA)
FTA uses a top-down approach, breaking down a problem into contributing causes in a tree-like structure. It is widely used in engineering and risk management.
5. Pareto Analysis
Based on the 80/20 rule, this method helps identify the few key factors (20%) causing the majority (80%) of problems. It prioritizes which issues require immediate action.
Developing a Root Cause Analysis Template
A structured template ensures consistency and thoroughness in RCA investigations. Below is a detailed template that organizations can use.
1. Problem Statement
Clearly define the problem in a concise manner.
What happened?
Where did it happen?
When did it occur?
Who was affected?
What are the consequences?
Example:"Production Line 3 experienced an unexpected shutdown on March 5, causing a 4-hour delay in delivery."
2. Impact Analysis
Evaluate the impact of the issue:
Operational Impact: Delayed production, increased workload, equipment downtime.
Financial Impact: Loss of revenue, repair costs, overtime expenses.
Customer Impact: Delayed shipments, potential loss of business.
3. Data Collection
Gather relevant data related to the issue.
Reports, logs, and records
Incident history
Employee interviews
Machine performance data
Supplier feedback
This step helps ensure that the RCA is based on facts, not assumptions.
4. Root Cause Identification
Use one or more RCA techniques to analyze the data and determine the root cause.
Apply 5 Whys for simple problems.
Use Fishbone Diagrams for complex issues.
Conduct FMEA for risk assessment.
5. Corrective and Preventive Actions
Once the root cause is identified, develop corrective actions to fix the problem and preventive actions to ensure it doesn’t happen again.
Short-term Fixes: Immediate actions to resolve the current issue.
Long-term Solutions: Process improvements, training, policy changes.
Example of Corrective Action:"Replace the faulty cooling fan on the machine."
Example of Preventive Action:"Implement a routine maintenance schedule to inspect and replace cooling fans before failure."
6. Implementation Plan
Outline the steps needed to execute the corrective and preventive actions.
Who is responsible?
What is the timeline?
How will success be measured?
7. Verification and Follow-Up
Once actions are implemented, evaluate their effectiveness.
Did the problem recur?
Are the preventive measures working?
Are there additional improvements needed?
Continuous monitoring ensures that RCA efforts lead to sustainable improvements.
Best Practices for Effective RCA Implementation
To maximize the effectiveness of RCA, follow these best practices:
1. Encourage a No-Blame Culture
RCA should focus on solving problems, not assigning blame. A culture of openness allows employees to report issues without fear.
2. Involve Cross-Functional Teams
Different perspectives from various departments help uncover hidden factors contributing to a problem.
3. Use Data-Driven Analysis
Base your RCA on measurable data rather than assumptions to ensure accurate conclusions.
4. Document Every Step
Keeping detailed records of RCA investigations helps track progress and serves as a reference for future issues.
5. Continuously Improve Processes
RCA should not be a one-time exercise. Regularly reviewing and refining processes ensures long-term success.
Conclusion - Root Cause Analysis Template
Root Cause Analysis is a powerful tool that enables organizations to address problems at their core, prevent recurrence, and drive continuous improvement. By using a structured RCA template, teams can systematically analyze issues, implement corrective actions, and enhance overall operational efficiency.
By following best practices and adopting the right RCA methodology, businesses can foster a culture of problem-solving and continuous improvement, leading to sustainable growth and customer satisfaction.
Root Cause Analysis can sometimes be referred to as root cause analysis template, root cause analysis format, root cause analysis templates, root cause investigation template, root cause analysis form template and root cause analysis template word
Subscribe and share your thoughts and experiences in the comments!
Professional Project Manager Templates are available here
Hashtags
#RootCauseAnalysis #ProblemSolving #BusinessEfficiency #RootCauseAnalysisTemplate #ContinuousImprovement #ProcessOptimization #QualityControl #ManufacturingExcellence #LeanManagement #SixSigma #WorkplaceSafety #OperationalExcellence #RiskManagement #ProductivityTips #BusinessSuccess #PreventiveMaintenance
Comments